TEMA 9 SOLDADURA POR PUNTOS DE RESISTENCIA
Una vez mas nos vemos realizando una entrada sobre otro tipo de soldadura y en este caso sera sobre la soldadura por puntos de resistencia asique bloggers poneros comodos que arrancamos y esto no se detiene, a continuacion pondre el contenido de la entrada, espero que os guste:
-Soldadura por puntos de resistencia;
-Procedimiento de soldeo por puntos de resistencia;
-Soldeo por puntos de resistencia a una cara;
-El equipo de soldadura por puntos de resistencia
MULTIFUNCIÓN;
-Tratamiento térmico de las deformaciones concentradas;
-Tratamiento térmico de las deformaciones extendidas;
-Uso del equipo multifunción para la extracción de golpes:
-Soldeo de roscas, setas y otros elementos de fijación de
amovibles
Os haré una breve explicación de la soldadura por puntos de resistencia para ir entrando en calor.
La soldadura por puntos es un método de soldadura por
resistencia que se basa en presión y temperatura, en el que se calienta una
parte de las piezas a soldar por corriente eléctrica a temperaturas próximas a
la fusión y se ejerce una presión entre las mismas. Generalmente se destina a
la soldadura de chapas o láminas metálicas, aplicable normalmente entre 0,5mm y
3mm de espesor.
El soldeo por puntos es el más difícil y complicado de los
procedimientos de soldadura por resistencia. Los materiales bases se deben
disponer solapados entre electrodos, que se encargan de aplicar secuencialmente
la presión y la corriente correspondiente al ciclo produciendo uno o varios
puntos de soldadura.
Se trata del proceso de soldadura por resistencia más
conocido. Generalmente se destina a la soldadura de chapas o láminas metálicas.
La soldadura se limita a uno o varios puntos en los que las dos piezas solapan
una con otra. Como norma se usan las puntas de los electrodos.
Después de esta breve introducción os explicare el procedimiento de este tipo de soldadura
La soldadura por puntos de resistencia es un proceso de
generación de calor bastante simple: el paso de la corriente a través de una
resistencia genera calor. Este es el mismo principio usado en la operación de
resistencias en espiral. Además de las resistencias brutas, las resistencias
constantes también desempeñan un papel importante. Las resistencias constantes
se ven influenciadas por las condiciones de la superficie (aspereza, limpieza,
oxidación y enchapados).
La fórmula general de generación de calor para soldado por
resistencia es:
Calor = I2
x R x t x K
Donde "I" es la corriente de soldadura a través de
las piezas de trabajo, "R" es la resistencia eléctrica (en ohmios) de
las piezas de trabajo, "t" es el tiempo de soldado (en hertz,
milisegundos o microsegundos) y "K" es la constante térmica. La
corriente de soldadura (I) y la duración de la corriente (t) se controlan por
el suministro de energía del soldado por resistencia. La resistencia de las
piezas de trabajo (R) es una función de la fuerza de la soldadura y los
materiales utilizados. La constante térmica "K" puede verse afectada
por la geometría de la pieza, la colocación y la fuerza de la soldadura.
Los valores de la resistencia bruta y constante de las
piezas de trabajo, los electrodos y sus interfaces provocan y afectan la cantidad
de calor generado.
Los materiales a soldar (chapa), se disponen solapados entre
los electrodos, cuando se aplica una presión que permite el óptimo contacto
eléctrico, se hace pasar una corriente eléctrica de bajo voltaje y elevada
intensidad, durante un tiempo “t” determinado. El punto de soldadura se
localiza debajo de los electrodos, por ser el área donde la resistencia es
mayor, la forma de la zona soldada la podemos asemejar a un círculo (visión
planar), o a una elipse (visión transversal). Este tipo de soldadura se aplica
principalmente en la industria del automóvil, gama blanca y mobiliario metálico,
aunque se está igualmente aplicando en la industria aeronáutica.
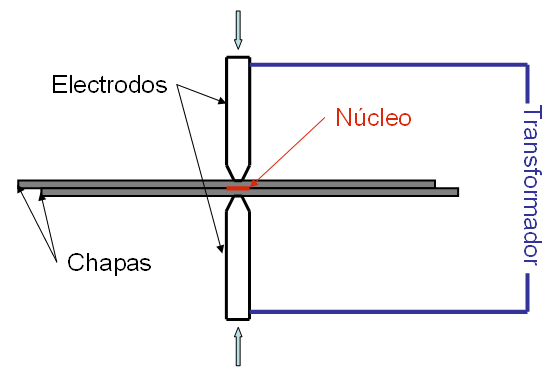
Pondre una foto de los distintos tipos de electrodos que se usan en este tipo de soldadura para tener una idea de como son:

explicado el metodo de soldeo general, me meto de lleno en la soldadura por puntos a una cara metodo de soldadura a una cara
Para realizar una soldadura a una única cara, deberemos hacer, en primer lugar, y al igual que siempre que se coje una maquina de soldar programar la máquina.
Esta maquina genera mucho calor para producir la unión de dos piezas así que me viene muy bien para unir con el siguiente apartado que tratara de los tratamientos térmicos y su uso para las deformaciones
concentradas y extendidas.
Desde mi punto de vista la maquina multifuncion es una maquina muy util siempre y cuando se sepa usar bien y con cabeza puesto que la gran cantidad intensidad que circula por ella es peligrosa a continuacion os ponde un pequeño video de como se puede fabricar una en casa........be carefulllllll
Para realizar una soldadura a una única cara, deberemos hacer, en primer lugar, y al igual que siempre que se coje una maquina de soldar programar la máquina.
Después acercamos el electrodo a la superficie a soldar y
presionamos con bastante fuerza sobre la chapa, mientras que hacemos masa con
una pinza en una superficie metálica limpia de impurezas
A pesar de todo, la resistencia de la soldadura a una
cara es bastante limitada, por lo que resulta aconsejable emplear otros métodos
que nos asegurasen una mayor resistencia y con ello evitar posibles daños colaterales
ahora me gustaría explicaros las partes de la maquina para que quede mas o menos claro que es cada cosa así que no se me ocurre mejor idea que poner un par de fotos y que lo veáis vosotros mismos, espero que os sirvan de ayuda para saber los elementos de la maquina MULTIFUNCION
Los electrodos:
Los electrodos se fabrican de un material que es buen conductor eléctrico y térmico (normalmente son aleaciones de cobre-cromo), y tienen una alta resistencia mecánica para que no se deformen con la presión
Fuente de energía:
Es un transformador de corriente alterna, capaz de proporcionar una gran intensidad eléctrica con una baja tensión de salida
Panel de control:
Desde el panel de control se regulan los parámetros de la soldadura, es decir, la intensidad, el tiempo, etc
Es un transformador de corriente alterna, capaz de proporcionar una gran intensidad eléctrica con una baja tensión de salida
Panel de control:
Desde el panel de control se regulan los parámetros de la soldadura, es decir, la intensidad, el tiempo, etc
Cabezal o también se le puede llamar pistola de soldadura:
Su misión es sujetar lo electrodos y esta conectada a la fuente de energía (transformador)
Esta maquina genera mucho calor para producir la unión de dos piezas así que me viene muy bien para unir con el siguiente apartado que tratara de los tratamientos térmicos y su uso para las deformaciones
concentradas y extendidas.
Lo primero que hay que explicar es que es un tratamiento térmico que no es mas que un conjunto de
operaciones de calentamiento y enfriamiento, bajo condiciones controladas de
temperatura, tiempo de permanencia, velocidad, presión, de los metales o las
aleaciones en estado sólido, con el fin de mejorar sus propiedades mecánicas,
especialmente la dureza, la resistencia y la elasticidad. Los materiales a los
que se aplica el tratamiento térmico son, básicamente, el acero y la fundición,
formados por hierro y carbono. También se aplican tratamientos térmicos
diversos a los cerámicos.
Tratamiento térmico de las deformaciones concentradas
Cuando una chapa, pongamos como ejemplo el capo de un coche,
se deforma, esta lo puede hacer concentrada (hacia dentro), o extendida (hacia
afuera), en el primer caso, todas las tensiones de la chapa se unen en el
centro de la deformación, mientras que en el segundo caso, las tensiones se
encuentran en los bordes del golpe.
En primer lugar hablare de una deformación concentrada, como
dije, vamos a ejemplificar en capo de un coche, lo primero que debemos de hacer
es de identificarla, normalmente, este tipo de golpes se encuentran cerca de
los nervios, o lineas de acumulación de tensión de la carrocería, los cuales,
no dejan que la deformación crezca en tamaño, por lo que al hundirse en metal
hacia adentro, se estira en su parte central, ya que en sus bordes no puede
expandirse porque los nervios se lo impiden.
Para que ese material estirado que tenemos en el centro de
la deformación se contraiga para poder devolverle a la chapa a su estado de
reposo original y sus características de rigidez y dureza, debemos de aplicarla
un tratamiento térmico, este tratamiento consistirá en aplicar calor y
seguidamente frió de forma brusca (agua aunque lo mejor sería un líquido
aintioxidante) para que el metal se contraiga, y obtenga su estado podemos
utilizar el conjunto de soldadura oxiacetilénica o la multifunción
Para ello debemos de calentar con la maquina multifuncion y
el electrodo de cobre en la pistola, hasta que la chapa se ponga de color rojo
cereza, a continuación, debemos enfriar
rapidamente el punto que hemos dado, se hara por la parte interior del golpe ya
que es la que se ha estirado y se hara repetidas veces
Gracias a esto aliviaremos las tensiones que tiene acumulada
la chapa por culpa de la deformación en el centro de la misma, y después
podremos extraer la abolladura
Tratamiento térmico
de las deformaciones extendidas
A diferencia del anterior, en esta deformación existe una
extensión del material, es decir, se ha dado de si, lo que hace que carezca de
rigidez por lo que se hace blando
Normalmente, estos tipos de deformaciones se producen en
lugares en los que no existen nervios, o también llamadas líneas de acumulación
de tensiones, como pueden se el paño de una puerta, en la que la deformación ha
sido amplia, debido a esa amplitud, todas las tensiones del golpe (deformación
del material), se han extendido hacia el exterior, justo a los bordes en los
que finaliza.
Identificar este tipo de deformaciones es simple, basta con
dar un pequeño punto de soldadura con la maquina multifunción, y sin tener que
dar uso al martillo de inercia, tirar hacia ti, en ese momento se puede sentir
como la chapa da sensación de ser blanda, de no estar rígida, además se puede
ver que es una deformación amplia, la cual si tiramos mas de ella la podríamos
dejar en sus sitio, aunque la chapa seguiría teniendo poca rigidez, por lo que
hay que tratarla térmicamente.
Para arreglar esto, tenemos 2 formas de procede, una de ellas
es creando un entramado de puntos de soldadura con la pistola de la
multifuncion y un electrodo de cobre, para darle calor y la otra es utilizando
un carboncillo en la punta de la pistola de la multifuncion; en ambos casos debemos
de aplicar el calor de fuera hacia adentro, ( desde el final del golpe hasta el
centro del golpe), que es donde mas tensiones se acumulan
En el caso de utilizar el electrodo de cobre, deberemos de
hacer un entramado de puntos, con una intensidad en la maquina alta, para que
se caliente bien la chapa, a continuación presionamos el botón de la pistola hasta
que la chapa coja un color rojo cereza en el lugar del punto, después separamos
el electrodo y le aplicamos frio rápidamente, de esa forma el metal tiende a
encogerse.
Definición de Esfuerzos Residuales
Uno de los principales problemas a los que se enfrenta el mundo
del metal es la acumulación de esfuerzos o tensiones que provocan la
deformación y la pérdida de la estabilidad dimensional. Fabricantes de aceros,
de máquina-herramienta, caldererías, fundiciones, empresas de
mecanizado, etc pueden experimentar problemas con la retención de tolerancias
dimensionales en la producción de sus piezas.
Podemos definir las tensiones residuales como cualquier
esfuerzo en un cuerpo elástico que se encuentre libre de fuerzas o
restricciones externas y de cambios o gradientes de temperatura.
Los esfuerzos, cuando no son iguales, pueden ocasionar
deformaciones del material. Grandes esfuerzos en un lado de la pieza provocan
movimiento o deformación. Si los esfuerzos son iguales a lo largo de toda la
pieza, se compensan y no hay deformación. Si el desequilibrio es demasiado
grande, la pieza jamás volverá a su condición anterior.
En los esfuerzos residuales hay dos componentes a tener en
cuenta: tensión y compresión. Las leyes de la física y las matemáticas exigen
un equilibrio entre la magnitud de compresión y la de tensión.
Desafortunadamente, en el trabajo con el metal, no hay un equilibrio uniforme.
La meta es producir un buen componente metálico o una
estructura con bajos esfuerzos residuales. Esto requiere un sistema para el
alivio o la reducción de estas tensiones con el fin de evitar futuros daños en
el material.
En el mundo del deporte encontramos un ejemplo muy
clarificador: si un deportista sufre un calambre o una distensión muscular, el
primer tratamiento recomendado es un masaje; si no se lleva a cabo, ese tirón
muscular puede convertirse en una fisura o rotura de fibras en un plazo más o
menos corto. Con el metal sucede lo mismo: las deformaciones internas del
material pueden transformarse en microfisuras que con el paso del tiempo se
traducirán en grietas en el exterior de la pieza.
Tratamiento de los esfuerzos residuales
Para tratar de devolver a la estructura metálica interna su
forma ideal, hay que introducir energía dentro del metal. El estabilizado por
tratamiento térmico es el método más conocido pero no el único.
El Estabilizado es un tratamiento térmico que consiste en
hacer desaparecer las tensiones internas que derivan de la fundición, soldadura
o mecanizado de los materiales. Para ello tratamos el material con un aumento
de calor progresivo, un mantenimiento homogéneo y un descenso igualmente progresivo.
En el tratamiento por horno, las temperaturas altas reducen
las tensiones en el material. Este tipo de alivio de esfuerzos, aunque
generalmente resulte efectivo, tiene varios defectos y limitaciones. El costo
es elevado, el proceso es de larga duración y frecuentemente da por resultado
el deterioro de las propiedades de los materiales.
·Tratamiento térmico de las deformaciones concentradas:
Se emplea para devolver un material a su forma original
mediante la aplicación de calor cuándo haya sufrido un recogido.
Al aplicar calor en el punto que concentra más tensión se va
liberando dicha tensión, lo que nos permite ir moldeando la deformación hasta
conseguir que la pieza vuelva a su forma original aunque haya vuelto a sus
forma inicial las características del material serán distintas a las de origen
·Tratamiento térmico de las deformaciones extendidas:
Si un material ha sufrido un estiramiento , podemos liberar
tensión mediante calor gracias a este equipo, con el objetivo de devolver la
pieza a su forma original.
Se aplicará de forma similar al apartado anterior, pero por
la parte externa del hundimiento.
Hay que mencionar que cualquier opción de las citadas
anteriormente hay que mirar si compensa el tiempo de trabajo estipulado para la
realización de la tarea y el resultado final o si por el contrario es mejor
sustituir la pieza por completo
Cambiando un poco de tema, esta maquina tiene tantos usos que nos puede ayudar incluso a sacar golpes de un vehículo de la manera siguiente y hablare tambien de soldeo de roscas arandelas y demás útiles que nos servirán en el trabajo
Hay muchas formas de sacar golpes de un vehículo pero no todos sirven para todos los sitios, bien sea por el espacio de acceso o por el proceso a realizar después una vez sacado el golpe. Un método muy útil es el de extraer golpes mediante soldadura.
En efecto, este procedimiento se lleva a cabo con un equipo
como el mostrado anteriormente que está formado por una máquina especial de
soldadura con la que se pueden soldar a la superficie de la chapa cualquiera
de los tipos de puntas que se pueden ver en la siguiente foto. Estas puntas
pertenecen a la dotación del mismo equipo.
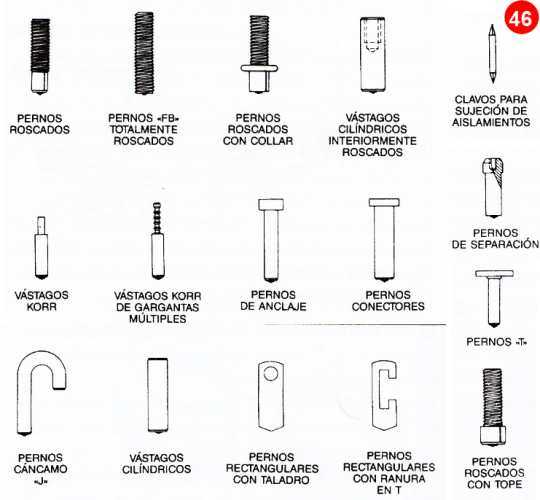
El elemento más importante es la pistola de soldar que puede
ser de diversos tipos, según cada una de las marcas existentes en el mercado.
Una vez vista su constitución pasemos a dar unas
instrucciones sobre el uso de estos aparatos que son muy importantes en
cualquier taller de chapa de automóviles porque son muchos los coches
que reciben estos pequeños golpes en las planchas de revestimiento, golpes que
son lo suficientemente profundos como para no poder ser disimulados con las
masillas y cuya reparación a mano resultaría muy entretenida y difícil, muchas
veces por la dificultad de picar desde el interior.
Desabollado por soldadura de clavos o arandelas, diferentes
modelos de pernos
Las operaciones a realizar son las siguientes y por el mismo
orden:
En la zona en la que se encuentra la abolladura o la rayada
con hundimiento se procede a limpiarla escrupulosamente para sacar la
pintura y las capas protectoras con el fin de dejar la plancha a la vista.
Se trata ahora de soldar un clavo o arandela de cobre en la
parte más superficial de la plancha, de manera que no queme excesivamente su
material. Esto se consigue dando un golpe
rápido al interruptor de la máquina, con lo que se logra una descarga eléctrica
de tal manera que el clavo o arandela queda fuertemente soldado en la plancha.
Ahora bien, es importante tener en cuenta que al interruptor hay que darle una
orden muy rápida.
La última operación consiste en el estirado. Si se ha
soldado un clavo, en el martillo deslizante se instala una especie de
portabrocas, que puede sujetar con
firmeza el clavo. Si se ha soldado una tuerca se deberá hacer uso de un gancho. Estos utillajes se aplican a la
punta del martillo deslizante y desde él se puede picar a contragolpe para
sacar la abolladura con bastante comodidad.
La operación final consiste en, una vez reparada la
abolladura, sacar el clavo soldado o la arandela. En el primer caso saca el clavo con la ayuda de unas tenazas imprimiendo
un giro a las mordazas de la herramienta y, de la misma forma, con un gancho,
para las arandelas. Con este sistema el operario se ahorra desguarnecer o
destapizar la pieza que se ha de reparar, conseguirá sacar bollos en aquellos
lugares donde no llega una palanca y, con práctica, con este sistema podrá
dejar anulada por completo una abolladura, de una forma prácticamente perfecta,
cosa que no es nada fácil por otros procedimientos. Sin embargo, sus
posibilidades no son ilimitadas y el sistema no nos va a servir para sacar
abolladuras de gran extensión ni tampoco nos permite trabajar con éxito en
zonas rígidas de la estructura como taloneras o montantes.
El uso de este sistema tiene que tener un aprendizaje previo
pues si, por ejemplo, soldamos demasiado un clavo y por descuido se nos pone al
rojo y posteriormente con el martillo deslizante le damos un contragolpe
excesivamente fuerte puede desprenderse el clavo llevando con él un trozo de
plancha rota. También se corre el riesgo de soldar demasiado el clavo y tener
dificultades para sacarlo hasta el punto de que se tenga que utilizar la
esmeriladora, con lo que la reparación se complica. Éstos son los sistemas de
desabollado por los procedimientos de taladrado o soldadura.
Ahora me gustaría hacer un pequeño inciso sobre otra forma de soldar que tiene esta maquina multifunción y con ello terminar de ver y con ello de demostrar la gran variedad de aplicaciones que tiene esta maquina multifunción, se trata de otras dos formas de soldar que se pueden realizar con ella:
Soldadura por impulso. Es una variante de de la soldadura por puntos. Mientras que en la soldadura normal la corriente circula continuamente durante un tiempo determinado y luego se interrumpe manual o automaticamente. En la soldadura por impulsos la corriente circula intermitentemente en forma de impulsos que se regulan previamente, de esta forma se puede soldar espesores mas gruesos gracias a la refrigerancion de los electrodos. La pieza se calienta localmente por medio de un impulso eléctrico (hasta nueve impulsos) de baja tensión gracias al cabezal de soldadura. Esta técnica no requiere realizar una presión fuerte en el momento de la soldadura, por lo que la estética de la cara visible permanece inalterada a la vez que se garantiza una buena calidad de la soldadura.
Soldadura por roldanas :El
proceso de soldadura por roldanas o también conocido como soldadura de costura
es una adaptación del proceso de soldadura por puntos que forma parte de los
procesos de soldadura por resistencia. La costura se forma debido a una serie
de soldaduras por punto que se superponen mediante el giro de los electrodos
circulares o roldanas, que son los encargados de ejercer presión y corriente,
para formar una superficie continua en la unión apretada. Se produce la
soldadura en las superficies de contacto de dos metales similares
Desde mi punto de vista la maquina multifuncion es una maquina muy util siempre y cuando se sepa usar bien y con cabeza puesto que la gran cantidad intensidad que circula por ella es peligrosa a continuacion os ponde un pequeño video de como se puede fabricar una en casa........be carefulllllll
Espero que os haya entretenido esta entrada sobre la maquina multifuncion y sus multiples nunca mejor dicho posibilidades de trabajo.
Con esto me despido hasta la próxima entrada del blog un saludo blogguerssssssssssss
No hay comentarios:
Publicar un comentario